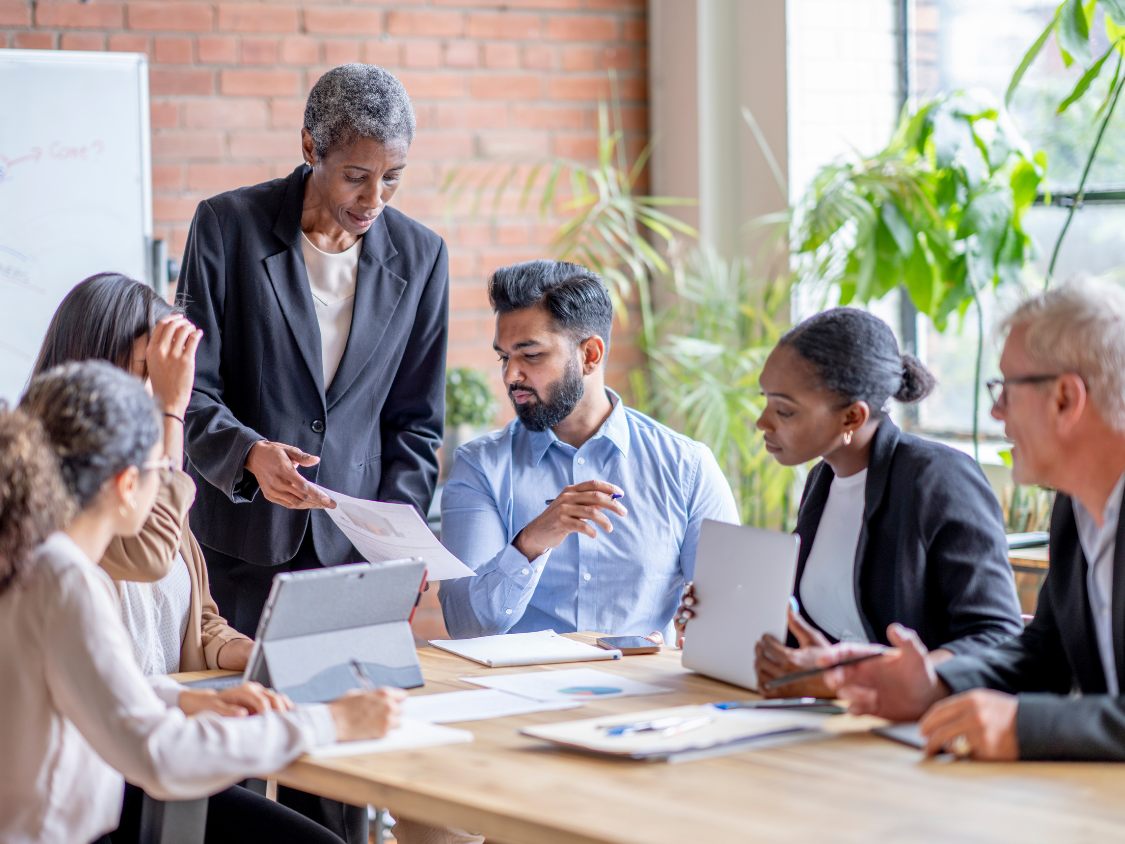
Stepping into a new role as a Labeling Director or Manager can be overwhelming. With budget constraints, compliance pressures and efficiency goals to live up to, it’s often quite the juggling act. Whether you’ve inherited a well-oiled machine or a chaotic system held together by outdated processes, your first 90 days are crucial for assessing the current labeling procedure and setting a plan for improvement.
To help you hit the ground running, we’ve outlined the key areas to assess as you evaluate your company’s labeling processes.
1. Audit the Current Labeling System
First thing’s first, you need to audit the existing system in place. It’s crucial to understand exactly what you’re working with before making any changes. A good starting point is to conduct a thorough audit of:
- Labeling software & technology – Is the system modern, efficient, and scalable? Or are employees struggling with outdated software?
- Compliance & regulations – Are current labels meeting industry and regional regulatory requirements?
- Label design & standardization – Are templates standardized, or does every department create its own?
- Print infrastructure – Are printers and hardware reliable, or are production delays caused by breakdowns and inconsistencies?
2. Identify Bottlenecks & Pain Points
The next step is to speak with key stakeholders—including production managers, quality assurance teams, and IT—to understand labeling-related challenges. Some common issues that people come to us to solve are:
- Slow label approval processes
- Inconsistent or non-standardized labels
- Frequent labeling errors leading to rework and even recalls
- Difficulty integrating labeling with other business systems (ERP, WMS, MES)
- Expensive and lengthy processes to make mass label changes
- Lack of or insufficient audit trails
3. Evaluate Compliance & Risk Factors
Labeling mistakes can result in costly recalls, compliance violations, and reputational damage–never mind the potential threat to life! As a result, it’s important to ensure that:
- Labels adhere to all regulatory requirements for your industry (e.g., FDA, EU MDR, GHS, etc.).
- Version control is in place to track and manage label changes.
- There’s an approval process that prevents unauthorized changes.
4. Is Your System Future Proof?
Compare your company’s labeling approach with industry leaders. Are you leveraging cloud-based labeling, centralized data management, automation and AI? If not, it might be time to consider an upgrade. Technology is changing fast, with AI and automation leading the way–don’t get left behind!
5. Gather Insights from End Users
One of the best ways to assess your system and identify inefficiencies is by talking to those who use the system daily. Ask:
- How easy is it to create, update, and print labels?
- What common issues do they face?
- What improvements would make their jobs easier?
6. Make the Business Case for Improvement
Finally, if your assessment reveals gaps, you may need to advocate for a new system. Investing in a new system can be costly but the long-term ROI and safety of end users is crucial. Build a case by highlighting:
- Cost savings from reduced errors and rework.
- Improved compliance and risk reduction.
- Increased efficiency through automation and integration.
Next Steps
Your first 90 days should give you a clear picture of the strengths and weaknesses of your company’s labeling process. Whether you decide to optimize the existing system or implement a new one, the key is to act strategically—gather insights, build a strong case, and drive change that enhances efficiency, compliance, and scalability.
Wondering where to go from there? We’ve put together a blog on choosing the right solution to suit your organization here. Alternatively, if you need guidance with evaluating or upgrading your labeling system? Our labeling and artwork management experts are ready to help you transform your business processes with the help of our innovative cloud-based software, leading the way in the labeling and artwork software space.
Our software, Veraciti, utilizes AI to simplify and streamline the migration process, so the days of stress headaches from painful migration processes are officially over. Not to mention, Veraciti features a variety of automation tools to prevent errors and recalls and ensure compliance and faster speed-to-market. Read our recent blog here to understand some of the most common challenges with labeling and artwork software and how to overcome them with software like ours. Alternatively, learn more about the key benefits of labeling and artwork software here.
Get in touch today to see what we can do for you at enquiries@kallik.com or call +44 (0) 1827 318100.