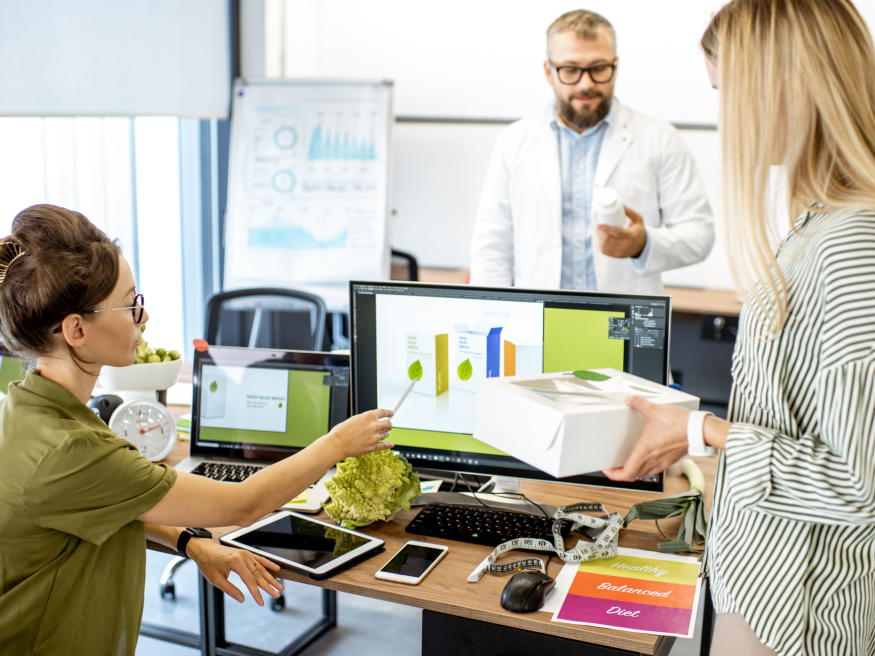
Forthcoming regulations (including the new EU MDR regulations coming into force May 2020) require labeling content to be published electronically in addition to print.
As companies seek to continuously differentiate themselves in established markets as well as gain entry into new territories, the increase in both volume and complexity of product and market variations will have a direct impact on labelling.
Transforming existing paper-based legacy artwork management systems and processes to a new digitally-driven environment are two concepts that can, in fact, work together to help highly regulated industries reduce the risk of non-compliance and costly product recalls.
Transforming your business with two concepts
Firstly, all parties or stakeholders, including regulatory, marketing and manufacturing must have access to the same system that masters the content – this means they must have access to the correct level of permissions in order to edit, modify and review the labelling content as needed.
Secondly, when much of the labelling content is held in a range of documents, emails, PDFs and printed documents, it can become difficult to construct, deconstruct and reuse labelling content.
These organizational challenges, therefore, need to be overcome, calling for the digitization of all labeling assets. Labeling and artwork processes have tended to be seen as more of a cost overhead rather than a core business activity. This can lead to systematic failures due to a lack of clear ownership, loosely defined decision-making processes and too much reliance on ‘tribal knowledge’.
In other cases, need to make repetitive ‘low-level’ decisions manually, where these could otherwise be easily automated can lead to fatigue and unnecessary errors. The end result can be costly product recalls potential fines and brand damage through non-compliance.
This is where the ‘business rules’ approach comes in – managing the decision-making process as a set of business rules allows for more responsive changes or additions to processes as this can be undertaken by business users as opposed to writing code. Whilst we could choose to implement a standalone business rules engine to automate many of the existing manual driven processes that often exist, we would still be left with the challenge of discovering and extracting the source content needed for each label variant.
The way we can overcome this is by digitalizing and versioning each of our labeling assets (logos, warning statements, images, etc.) and ensure that these are easily discoverable. We can then configure our business rules engine to find, and subsequently populate, each of the variable fields we may need on our labels depending on where the product is going to be sold and which local market legislation needs to be adhered to.
Seeing the opportunity in the EU MDR
Much of the medical device industry is quite rightly focused on understanding the impact of the legislative framework and being in a state of readiness to populate the EU equivalent of the GUDID, this being EUDAMED (European Database on Medical Devices) by May 2020. In addition, implementing the upcoming European Unique Device Identifier will require considerable investment and strategic planning for many organisations, so now is a good time to consider options for process re-engineering.
At Kallik, we see the EU MDR as an opportunity for organisations to review the effectiveness of their current labelling and artwork processes and how digitising supply chains can strengthen compliance and simplify evolution toward e-Labeling. Securely managing all product and prescribing-related information in a single version controlled environment enables unlimited composition, re-use and printing of any type of label anywhere. Furthermore, your labelling becomes ‘channel agnostic’, that is it can be delivered through multiple channels (web, mobile, social) as well as via the more traditional paper-based means of presentation.
Adopting labeling digitalization enables more robust regulatory submissions and ultimately increases the transparency of enterprise-wide review and approval processes. This can simplify the integration of extended supply chains and shorten time to market during periods of mergers and acquisitions.
Want to know more?
Whether you’re in the food and beverage, pharmaceutical, medical device, chemical, or even the cosmetic industry, our experts are ready to help you transform your labeling and artwork management with the help of our innovative software, leading the way in the labeling and artwork software space. Get in touch today to see what we can do for you at enquiries@kallik.com or call +44 (0) 1827 318100.