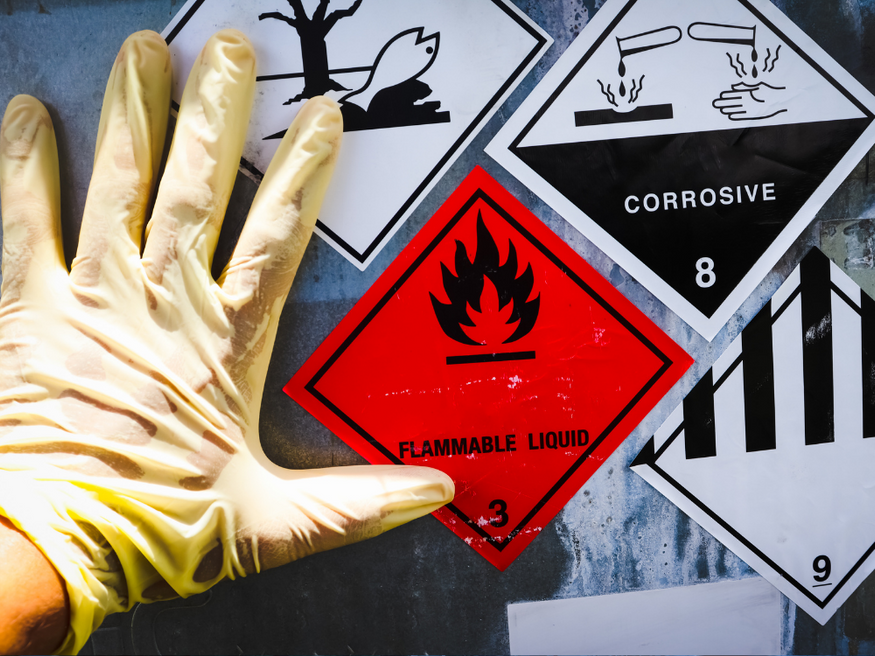
A Challenging Year for the Chemicals Industry
2020 has not been kind to the chemical industry with the challenges it has presented. The COVID-19 pandemic and the subsequent collapse in demand for oil has had a profound effect on the energy industry in particular. While the energy sector comprised 16% of the S&P 500 in 2008 according to Bespoke Investment Group, the energy industry today makes up a mere 2.5% of the S&P 500. The market has shifted in ways unprecedented a mere year ago.
The pandemic has also spotlighted the need for more sustainable solutions in the pending climate emergency. New sustainability legislation will undoubtedly move the goalposts for lubricant manufacturers. The proposed ‘Euro 7’ regulations will likely, according to FleetPoint, arrive in 2024/2025 and stipulate a 15% reduction in fuel consumption compared with 2019 numbers, followed by another 15% by 2030. Research is allegedly already underway to formulate low and ultra-low viscosity oils, helping to enhance fuel efficiencies.
Inefficiency is Everywhere
In an ever increasingly competitive world, speed to market is crucial; oil and lubricant manufacturers must stay ahead of the curve. The recent lack of demand need only increase efficiency so that no resources go to waste. Furthermore, new products require new labels, which must undergo a stringent review and approval process. It is vital that chemical companies do not allow this to slow the rate of new product introduction (NPI).
Companies which operate on a global scale with a large range of products must be able to manage the challenge of localisation. European products will need translations for over 20 languages on each pack, and translations will need to be updated in alignment with regulatory changes or formulation changes.
The lack of consistency in the approach to managing packaging and labeling across regions can lead to intensive, time consuming, manual processes, as well as duplication of effort which can be costly. It is not only market behaviour which factors into this, but more pertinently the differing regulations and languages between regions which make for a complex operation.
Moreover, product and label regulations can often be subject to change. Keeping on top of this manually through a process of email approvals and file digging can be incredibly time consuming. However, compliance is non-negotiable, with recalls incurring huge costs. Adherence to regulations can be ensured through adequate auditing of each stage of the approval process in one central location. Compliance need not hinder efficiency.
Dealing with third parties also hinders agility. Many chemicals companies outsource their artwork creation and updates to external agencies. Not only is the use of these agencies extremely costly, even if the change could be as minor as updating a claim statement or adding a new regulatory symbol, but it adds another handoff in an already complicated process. The artwork agency could take several weeks to create the artwork, and further rounds of amendments will likely be required after review internally which would lead to further back-and-forth.
Throw into this a complex network of third party printers, scattered across the globe. Chemicals companies who manufacture consumer facing goods such as engine oil will need to produce glossy consumer facing labels, which need specialist printing capability. Ensuring these globally distributed printers only have access to the most recent approved version of a label is key, but using manual processes such as emails to communicate changes means the chances of the wrong version being printed are high.
Potential counterfeiting must also be considered; the chemical industry is continually a victim of this. In order to combat this, many oil companies have created their own unique proprietary fonts which have been designed in a way which makes them difficult to copy. This makes their labels difficult to replicate, but it is entirely possible in a manual process that these fonts could be substituted for something similar, or worse, that the native artwork files could fall into the wrong hands.
These inefficiencies cost the chemicals industry not just in financial terms, but in terms of opportunities and competitive advantage. In a highly competitive sector that is already struggling, chemical companies cannot afford to continually make these errors and decrease their potential. The COVID-19 pandemic and the increasing awareness globally of the need to reduce oil consumption to combat the climate crisis have only emphasised the requirement for greater efficiency and innovation when it comes to chemical product management and labeling.
Automation and Control Drive Speed to Market
An intelligent cloud based end-to-end label management software provides the answer to many of these challenges. Not limited to the chemical industry, a true label management solution can prove highly beneficial to all highly regulated industries through cutting costs, decreasing compliance risks, and returning control to the company. Increased efficiency allows chemical companies to reach their full potential and excel in a highly competitive industry.
Perhaps the most significant way to increase efficiency is through automation. Artwork automation, foremost, vastly reduces and in some cases can regate the need for costly artwork agencies. Artworks can be produced and managed in-house, with little manual input. Changing a claim on a label, or even creating a brand new localised variant to tap into new markets is straightforward and can be achieved in minutes instead of weeks. Even before artwork creation, there are huge opportunities to automate the collation of the label data.
Through the use of intelligent rules, regulatory requirements for labeling can be pre-configured so that every label will always be populated with the correct regulatory content. This drives quality and compliance into the artwork creation process, reducing the number of rework cycles and getting labels approved more quickly. Furthermore, automated approval routing can drastically speed up the long winded approval process, whilst ensuring that the right people are involved. Automating as many manual tasks as possible allows employees to dedicate their time to more pressing or value-add tasks. Each of these factors enables companies to increase NPI, something which will prove highly valuable in the aftermath of COVID-19.
The standardisation of artwork assets and their containment to one central location supports ease of access and anti-counterfeiting. A centralised structure which is accessible across the globe at all times promotes cross-regional collaboration and allows for global consistency of resources.
Furthermore, third party printers can be granted access to the same software, ensuring that they always have the most up-to-date version of labels and artworks, minimising errors and compliance risks. This subsequently contributes to the quality and consistency of products.
With a fully audited end-to-end system, every step of the process is accounted for, making it easy to identify errors or discrepancies. This also increases the ability of managers to monitor performance, having employee’s tasks and approvals set out in front of them. By having all of these steps tracked and visible for reporting, it is easy to see the status of a label and identify any bottlenecks in the process, enabling managers to take action where required to remove any blockers to finalising critical artworks.
Don't Get Left Behind...
The chemical industry is only just starting to realise the value of having an end-to-end labeling and artwork management system, which can transform artwork and labeling processes by removing manual tasks and giving control and visibility of the entire lifecycle. Given the current challenges faced by the chemical industry today, now is the time to seize this opportunity. Working with a software provider who has real experience delivering to your industry, speaks your language, understands your labels and has a blueprinted methodology for global implementation projects for chemicals companies will make your journey to a more efficient artwork management process a smooth and successful one.
Want to know more?
Whether you’re in the food and beverage, pharmaceutical, medical device, chemical, or even the cosmetic industry, our experts are ready to help you transform your labeling and artwork management with the help of our innovative software, leading the way in the labeling and artwork software space. Get in touch today to see what we can do for you at enquiries@kallik.com or call +44 (0) 1827 318100.