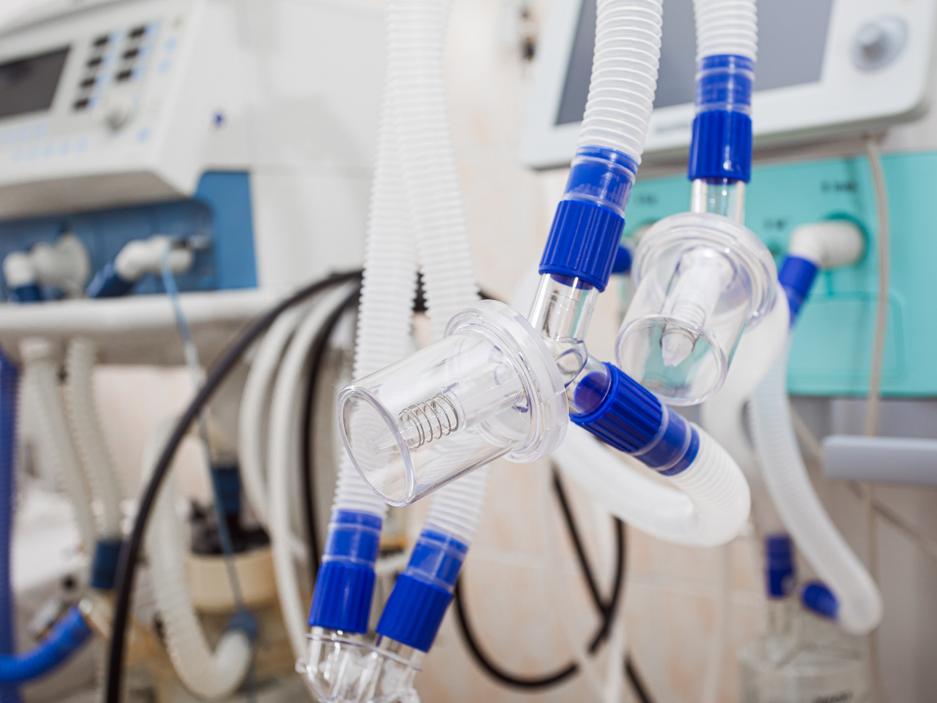
The UK has just over 8,000 ventilators, significantly fewer than the 30,000 the government estimates are needed to cope with the fallout from the peak of the Coronavirus epidemic. Clearly, the race is on for medical ventilator specialist manufacturers to ramp up production.
Manufacturers are being asked to close the gap, with firms like Dyson, Airbus, GKN, Rolls Royce, Megitt and others working on partnering with medical device manufacturers on new designs to meet the huge and unprecedented demand for the units.
But the danger is that these new entrants, very welcome as they are, may struggle with a key process: getting the product and package labeling elements correct and aligned with NHS needs.
And the inability to prove the required level of clinical evidence and correct labeling will ultimately prevent the new ventilators from getting to the NHS staff who need them in a timely manner, and time is of the essence.
What we can do as a supplier is to offer our expertise on this aspect. That’s because we have accumulated a great deal of experience in the medical device manufacturing space. We’ve helped our customers deal not just with national/international requirements, but the large amount of required text and graphics that must now be featured on individual labeling.
Based on our exposure to these issues, there are a number of practical measures you can take, in order to help you mount the quick and effective response to the current crisis required and get the new machines into the NHS in a timely, safe and acceptable manner. These are:
- Ensure that you are aware of the Government’s new regulatory exemptions as it relates to medical device manufacture during the current situation.The FDA has also updated their policy based on the current COVID-19 situation.
- Get up to date on which regulations you still need to comply with, namely EU Medical Device Regulation (MDR), US Unique Device Identification (UDI), and global product serialisation — but note that the former, which is formally due to take effect from 26 May 2020, may well be delayed, as the medical technology industry is lobbying for it to be postponed. This is a fast changing area, but we can help here, e.g. share current legislation information, best practice, and provide advice on how to navigate the rules with you if you’re not familiar with them.
- Leave nothing to chance. To meet the tough deadlines and ensure nothing derails your manufacturing schedule, introduce a Corrective/Preventative Action process (CAPA) to quickly identify any potential non-conformity or issue to quickly respond to issues wherever and whenever they might occur to assure the problem can never be experienced again.
Kallik is working hard to ensure that all of our customers are able to continue to perform their essential labeling and artwork management processes during this uncertain time. If you are looking to take new ventilators or other medical devices to market faster during this time by automating your labeling lifecycle, Kallik can get you up in running in weeks, not months.
We are also proud to be a UK listed supplier, helping the public sector during the coronavirus COVID-19 outbreak.
Stay safe and we will get through this together.
Want to know more?
Whether you’re in the food and beverage, pharmaceutical, medical device, chemical, or even the cosmetic industry, our experts are ready to help you transform your labeling and artwork management with the help of our innovative software, leading the way in the labeling and artwork software space. Get in touch today to see what we can do for you at enquiries@kallik.com or call +44 (0) 1827 318100.