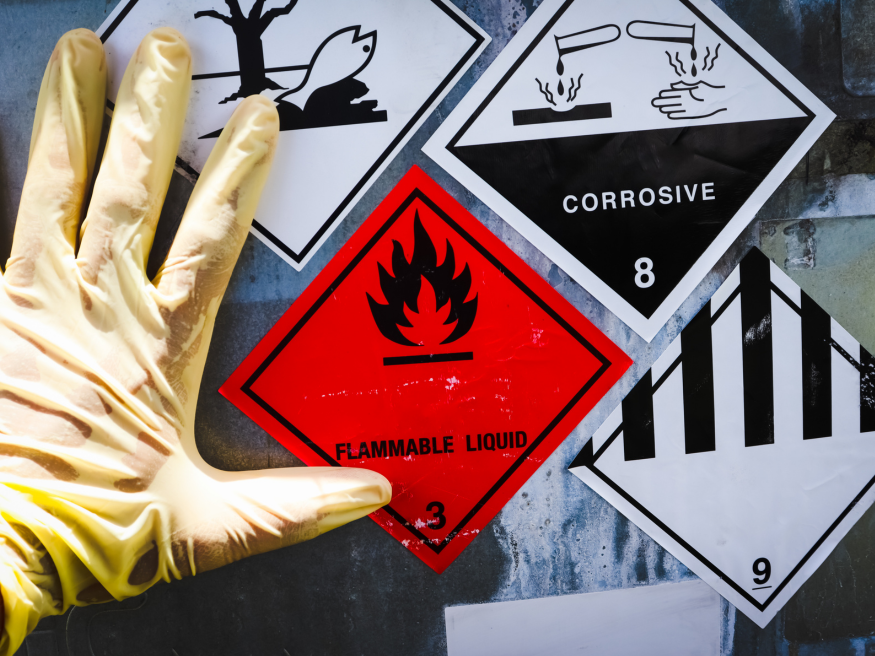
We recently caught up with a prominent executive from the chemicals sector to find out what they think are the important trends in their industry in 2020 and beyond. What we found: a real need to simplify the complexity of labeling management in their global industry so that ever-intensifying regulatory demands don’t crunch too hard on market growth.
Trust, transparency and, above all, the safety of process/supply-chain intermediaries and consumers is of paramount importance to the global chemicals industry. At the same time, increasingly stringent regulations about product/substance-based declarations, hazard warnings, and use of mandatory safety statements and symbols is definitely taking its toll on the supplier end; there are now so many regulated elements that must be carried on product packaging and labeling that they’re potentially starting to impinge on the market’s ability to execute. A specific area of concern here is the complexity. As an industry, we have to deal not just with new international, regional or country-specific requirements but the sheer volume of required text and graphics that must now be featured on individual labeling.
To maintain market authorization in each market and to uphold brand standards and market confidence, manufacturers must have 100% control over the quality, consistency, accuracy and currency of everything that appears on their labels and the legibility/user-friendliness of that content. In 2021, chemical products will need to carry a unique formula identifier (UFI), a 16-character alphanumeric code required on the label of any products that contain a hazardous mixture, assigning almost batch-specific traceability to chemicals. This will constitute a further obligation on manufacturers and brand owners to manage on their labeling, whether their products are destined for consumers or industry.
Regaining Control
Such is the scale of the challenge that the industry has been dialoguing with regulators about alternative approaches to help ease the burden. These suggested help-mates range from the use of market-agnostic pictograms for safety advice to the option to move finer detail to product inserts or online rather than have to try to fit them on to the smallest spray-can, or tube of adhesive. In future, it is more than possible that apps and scan-able QR codes will make it easier to link physical and complementary digital labeling, reducing the need to attach so much information directly onto products.
But that’s in the future. For now, when changes to labeling are required, or if errors or omissions to printed content are identified, companies risk having to recall products or re-label many thousands of items while also setting up to dispose of all the labels and instructional materials already printed. As well as being very costly — potentially running into tens of thousands of dollars each time current labeling stock is rendered obsolete— this often runs counter to existing organizational commitments around sustainability and social responsibility.
Whether a manufacturer’s chemical products are consumer-facing or designed for industrial use, regaining control over spiraling complexity requires that labeling can be tracked and managed on a global, enterprise-wide scale, and assembled in a structured way that makes lighter work of change and variant management.
Centralizing Labeling Management Capability
To get there, streamlining requirements and boosting control must start with a clear line of sight across everything that is going out to the market, anywhere in the world. This means creating a single source of labeling truth of approved, current label components. If anything changes — to the brand, to the product or its ingredients, or to regulatory requirements — it can be managed in a controlled and robust way from a single, central vantage point.
One of the biggest benefits of imposing centralized structure and control like this: it creates certainty. Certainty that the right information is going out on every product, every time, in every market. In this way, the manufacturer is able to maintain safety, compliance and market confidence, plus reduce the risk of product recalls, fines for mislabeling, and the high cost of labeling reprinting and reissue.
A centralized labeling management capability can also stop teams starting from scratch when just a small aspect of a label, such as a logo or listed substance, needs to be amended or replaced, enabling a much more efficient change process. The ability to create standardized labeling templates and treat each labeling item as a composite of pre-approved text or artwork components, eliminates unnecessary process duplication, leaving skilled professionals free to focus more of their time on the elements that do need to change.
Sensitivity Parameters & Smart Tools
Enterprise labeling management can also help transform the processes involved, for instance in discovering label inter-dependencies if requirements or other conditions change, as all global label activity is mapped and tracked. The central platform can also be used as a reliable look-up for latest country-specific requirements and sensitivities, and to calculate quickly the ramifications of a single change request. Sensitivity parameters and smart rules can also be set to ensure that required logos and symbols are included, and that important information is displayed in legible fonts.
The verdict’s clear: through automation of your complex labeling activity, our sector’s regulatory burden can become controllable.
Want to know more?
Whether you’re in the food and beverage, pharmaceutical, medical device, chemical, or even the cosmetic industry, our experts are ready to help you transform your labeling and artwork management with the help of our innovative software, leading the way in the labeling and artwork software space. Get in touch today to see what we can do for you at enquiries@kallik.com or call +44 (0) 1827 318100.